Process Engineering, Director or Associate Director, Japan New Plasma Facility Project
Jūsō-honmachi, ŌsakaOn the Global Manufacturing and Supply (GMS) team at Takeda, you’ll be part of a rapidly transforming industry that’s applying technology and data in new ways. Within our agile, innovative, people-centric organization, your work will matter every day as you use your skills to help us manufacture therapies for patients on our four platforms:
- Small Molecules
- Biologics
- Plasma
- Cell and Gene
As part of the GMS team, you'll have the opportunity to pursue unique experiences and build new skills, and you'll know that the work you do every day makes an impact — on our patients, our people, our planet, and on yourself.
By clicking the “Apply” button, I understand that my employment application process with Takeda will commence and that the information I provide in my application will be processed in line with Takeda’sPrivacy Noticeand Terms of Use. I further attest that all information I submit in my employment application is true to the best of my knowledge.
Job Description
ABOUT TAKEDA
“Better Health for People, Brighter Future for the World” is the purpose of a company. We aim to create a diverse and inclusive organization where people can thrive, grow and realize their own potential while enabling our purpose. We continue to innovate and drive changes that will transform the lives of patients. We’re looking for like-minded professionals to join us.
Takeda is a global values-based, R&D-driven biopharmaceutical leader. We are guided by our values of Takeda-ism, which has been passed down since the company’s founding. Takeda-ism incorporates Integrity, Fairness, Honesty, and Perseverance, with Integrity at the core. They are brought to life through actions based on Patient-Trust-Reputation-Business, in this order.
OBJECTIVES/PURPOSE
Own Process Equipment is “fit for purpose” for the manufacture of drug substance and drug products, meeting Regulatory, Quality, Capacity and EHS requirements
Main objectives (key services)
Technology selection
Capacity Modeling and Site Master Planning
Engineering and Equipment Design
Safety engineering design and management
“Factory Floor” Continuous Improvement/ Troubleshooting / System ownership
Own strategic preparation of sites for the future by introducing new process technologies such as robotics and delivering agile process engineering solutions
Provides leadership to all engineering disciplines during the development of the project requirements, scope, design (concept, basic, and detail), timeline, and budget#
The incumbent is responsible for improving existing equipment to minimize production downtime and provide leadership to all process equipment related investigations
Develop and implement strategies to ensure cost and time effective designs while ensuring innovation and adhering to user requirements while managing daily operational support
ACCOUNTABILITIES
Technology selection
Drive Cross functional stakeholder management with our Partners in Manufacturing e.g. Sciences and/or Pharmaceutical Sciences. Sponsor the evaluation and selection of new, state-of-the-art technologies and process equipment and applicable process equipment vendors (e.g. Robotics Single Use Technology)
Identify future industry trends and decide on strategies for process equipment/technologies
Own business case development for CAPEX investments in process equipment incl. Total Cost of Ownership (TCO) calculations
Manage Process Equipment Vendors and Architectural/Engineering firms in the delivery of CAPEX and OPEX projects in areas of responsibility
Capacity Modeling and Site Master Planning
Mentoring of Process Unit Operation Capacity models and identify capacity bottlenecks / constraints in GMP manufacturing processes / production process and in the utilities delivery systems
Apply knowledge of heat transfer, mass transfer, fluid dynamics, reaction kinetics to solve common process engineering problems
Engineering and Equipment Design
Own Front-End Engineering and Design activities in feasibility study and conceptual design phases
Sponsor Project Turnover Packages for Process Equipment are delivered to site and that critical engineering knowledge such as as-built drawings, operating and maintenance manuals, equipment and instrument data sheets, spare parts lists are maintained, remain accurate and up to date
Gather requirements from Stakeholders - such as from Quality, Manufacturing, Reliability, Maintainability, Automation, and EHS – to decide on Process Basis of Designs, specifications and designs for Process Equipment, Process Control Systems, Process Instrumentation and Process Safety Systems and Devices
Lead Scope of Work and RFx Packages for Process Equipment Vendors, Process Engineering Consultants, Architectural / Engineering services, Commissioning services and (Sub-) Contractors
Sponsor commissioning activities such as Factory Acceptance and/or Site Acceptance Testing of process equipment
With Partners in Engineering Validation mentor the Qualification and Validation activities for Process Equipment
SME Design Reviews of Process Equipment with Stakeholders, including Quality, Manufacturing, Utilities Operations, Maintenance, Calibration, Reliability, Automation
Safety engineering design and management
Conduct Process Hazard Analysis (e.g. PHA-Hazop) of hazardous manufacturing / production processes and incorporate improvements into the design of process equipment, process control, and process safety systems
Perform Design Reviews of all process equipment with relation to EHS and lead for the relevant changes
Own Investigations for process equipment and implement Corrective and Preventive Actions (CAPA)
“Factory Floor” Continuous Improvement/ Troubleshooting / System ownership
Provide leadership the Manufacturing and Maintenance departments with troubleshooting activities of Process Equipment on the factory floor
Owner continuous improvement activities for Process Equipment applying continuous improvement tools such as DMAIC, FMEA, RCA, identify improvements, design and implement improvements and sponsor 3rd level troubleshooting in collaboration with “Manufacturing” &” Manufacturing sciences”
Mentor Management of Change for Process Equipment in area of responsibility
Responsible for internal and regulatory Audits and Inspections
Engage in the Process Engineering Community of Practice (CoP) through sharing of best practices and lessons learned
DIMENSIONS AND ASPECTS
Technical Expertise:
Lead and mentor system/equipment specifications
Determine basic causes, and develop and then follow up on recommendations for corrective actions
Enable capabilities to perform troubleshooting on system/equipment
Lead customer service problems and recommend design improvements
Leadership:
Displays and drives Takeda culture of Takeda-ism, PTRB, safety, and quality into the organization
Be on the floor to study and train and recommend techniques to enable the team to improve existing equipment to minimize production downtime.
Good interpersonal skills and be able to work effectively and efficiently in a team environment as leader, mentor, trusted advisor.
Demonstrates strong communication skills to effectively communicate with all levels of professionals, both internal (local & global) and external
Coach, motivate, develop, recognize and mentor the engineering staff, including senior level engineers and managers. Being a mentor developing future leaders
Decision-making and Autonomy:
Decision making on organizational changes to build the required capacity/capabilities
Autonomy in decision making to the level of required alignment
Decision making of short/mid & long-term impacts
Interaction:
CAPEX Project Teams, Manufacturing Sciences, Quality, Manufacturing / Production, Utilities/Facilities Operations, Plant/Facilities/Utilities Engineering, Reliability Engineering, Maintenance, Calibration, Automation, EHS, Procurement / Purchasing, Equipment Vendors, Architectural / Engineering Services Companies, (Sub-) Contractors, Consultants
Innovation:
Generate innovative solutions to highly complex problems
Demonstrated problem solving skills to support resolution of Engineering, Manufacturing and/or Quality-related issues
Complexity:
Assess, analyze, advise, propose and direct improvements that will deliver greater productivity, capacity, reliability and compliance for the Process Engineering Department
Ensure compliance to all regulatory GMP, Safety and Environmental requirements
Shall interface with regulatory agency representative (e.g. FDA/EMA) as the site Process Engineering SME during internal and external audits and shall be able to defend current practices to such agencies
Strong skills to work in matrix organization with excellent interpersonal, communication, influencing, and negotiation skills required
EDUCATION, BEHAVIOURAL COMPETENCIES AND SKILLS
Engineering degree or equivalent required; for example, Chemical, Biochemical, Mechanical or Industrial engineering is preferred
Minimum 5 years of relevant experience
Expert of Process Unit Operations in Pharmaceutical Manufacturing
Leader of CAPEX project delivery and equipment acquisition processes
Mentor in applying process improvement methodologies such as DMAIC and Root Cause Analysis (RCA), and tools such as Failure Mode and Effects Analysis (FMEA)
Understanding of Good Manufacturing Practices (GMP)
Experience with leading expert for e.g statistical data analysts and data visualization tools
Experience in managing of all machines/lines/systems and all its components
SME of Process Unit Operations in Pharmaceutical Manufacturing
Expert of CAPEX project delivery and equipment acquisition processes
Fluency in English
Fluency in Japanese is preferred
Locations
Osaka (Juso), JapanWorker Type
EmployeeWorker Sub-Type
RegularTime Type
Full timeWorking at Takeda
-
Inclusion
Here, you will feel welcomed, respected, and valued as a vital contributor to our global team. -
Collaboration
A strong, borderless team, we strive together towards our priorities and inspiring mission. -
Innovation
Bold initiatives, continuous improvement, and creativity are at the heart of how we bring scientific breakthroughs from the lab to patients. -
Top Workplace
Recognized for our culture and way of working, we’re one of only 17 companies to receive Top Global Employer® status for 2024. -
Work-Life
Our people-first mission extends beyond patients to include their families, communities, and our own Takeda family. -
Empowerment
Through trust and respect, you will have genuine support from leaders, managers, and colleagues to do your best work.
We're Steadfast In Our Commitment to Four Key Imperatives
Patient
Responsibly translate science into highly innovative medicines and accelerate access to improve lives worldwide.
People
Create an exceptional people experience.
Planet
Protect our planet.
Data & Digital
Transform Takeda into the most trusted, data-driven, outcomes-based biopharmaceutical company.
Jobs for you
- Final Drug Product Quality Manager Thousand Oaks, California Category: Quality
- Head of Marketing Acquisition Bannockburn, Illinois Category: Sales and Marketing
- Head of Brand & Insights Bannockburn, Illinois Category: Sales and Marketing
- Portfolio Management and Improvement Lead Boston, Massachusetts, Zurich, Switzerland Category: Strategic Planning
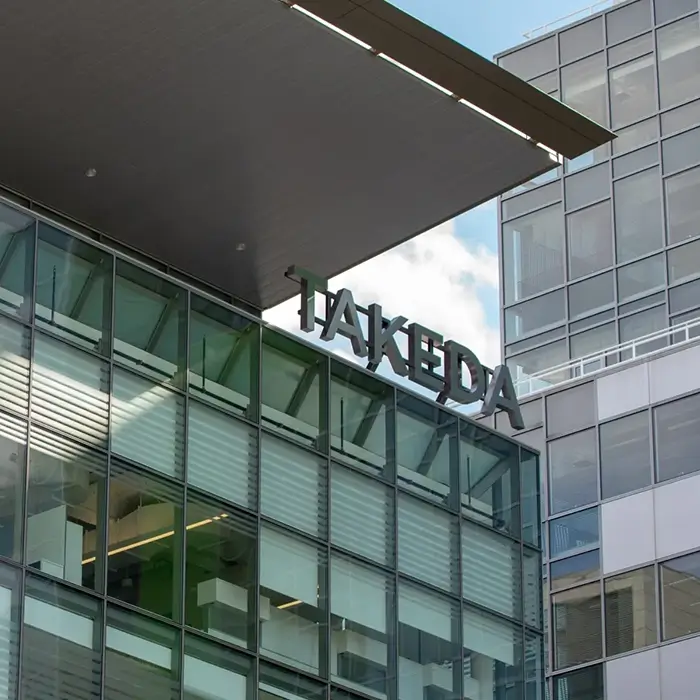
About our location
Join our talent community
Get customized job alerts sent right to your inbox. Plus, get the latest in company news and other important resources by signing up for our talent community.